Customer Story
Jimmy Fairly Lab Drives Efficiency and Sustainability with Satisloh’s E-Ticket System
When Jimmy Fairly’s Director of Lab Operations, Manuel Gonçalves, first joined in 2018, his mission was clear: create an efficient, high-quality assembly lab to support the company’s growing demand for stylish, responsibly produced eyewear.
Since the lab’s launch in 2019, it has rapidly scaled, now assembling 1,400 items daily to support over 148 Jimmy Fairly boutiques across Europe. However, as demand grew, so did the need for innovation to streamline lab processes and enhance sustainability. That’s when Manuel turned to Satisloh’s E-Ticket System.
Having maintained a strong connection with Satisloh since 2018, Manuel discovered the E-Ticket solution during a period of organizational change in late 2023.
The timing was ideal, and by April 2024, Jimmy Fairly Lab fully integrated Satisloh’s E-Ticket.
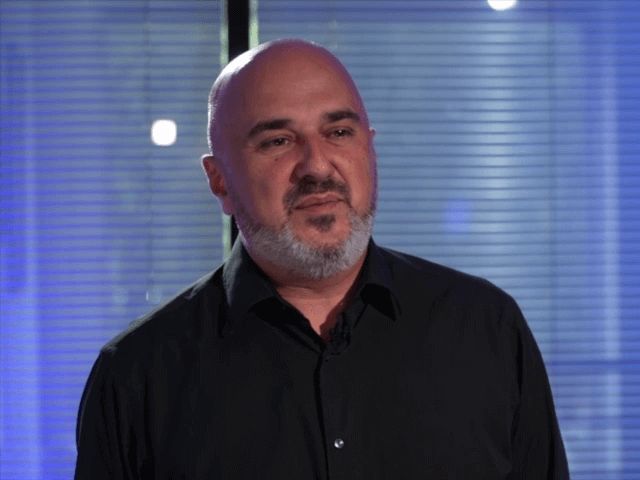
Download the entire success story here:
We were in the middle of an ERP and WMS change. Printing job tickets was coming back to the lab, meaning we would need an extra person for a non-value-added task. That’s when Xavier Bultez Satisloh VP Integrated Solutions introduced me to the E-Ticket System.
Manuel Gonçalves, Director of Lab Operations at Jimmy Fairly
A Swift, Seamless Implementation
Satisloh’s team provided hands-on support throughout the three-week integration period, enabling a quick and disruption-free rollout. The setup was smooth, with no impact on production. The Satisloh E-Ticket team was on board every step of the way, ensuring our templates and workflow matched our needs exactly.
The system’s flexibility and compatibility with the lab’s LensWare Software were pivotal to its success. After reviewing production orders and job ticket information, Jimmy Fairly Lab customized the E-Ticket templates to only display essential information, eliminating excess data and improving efficiency on
the shop floor.
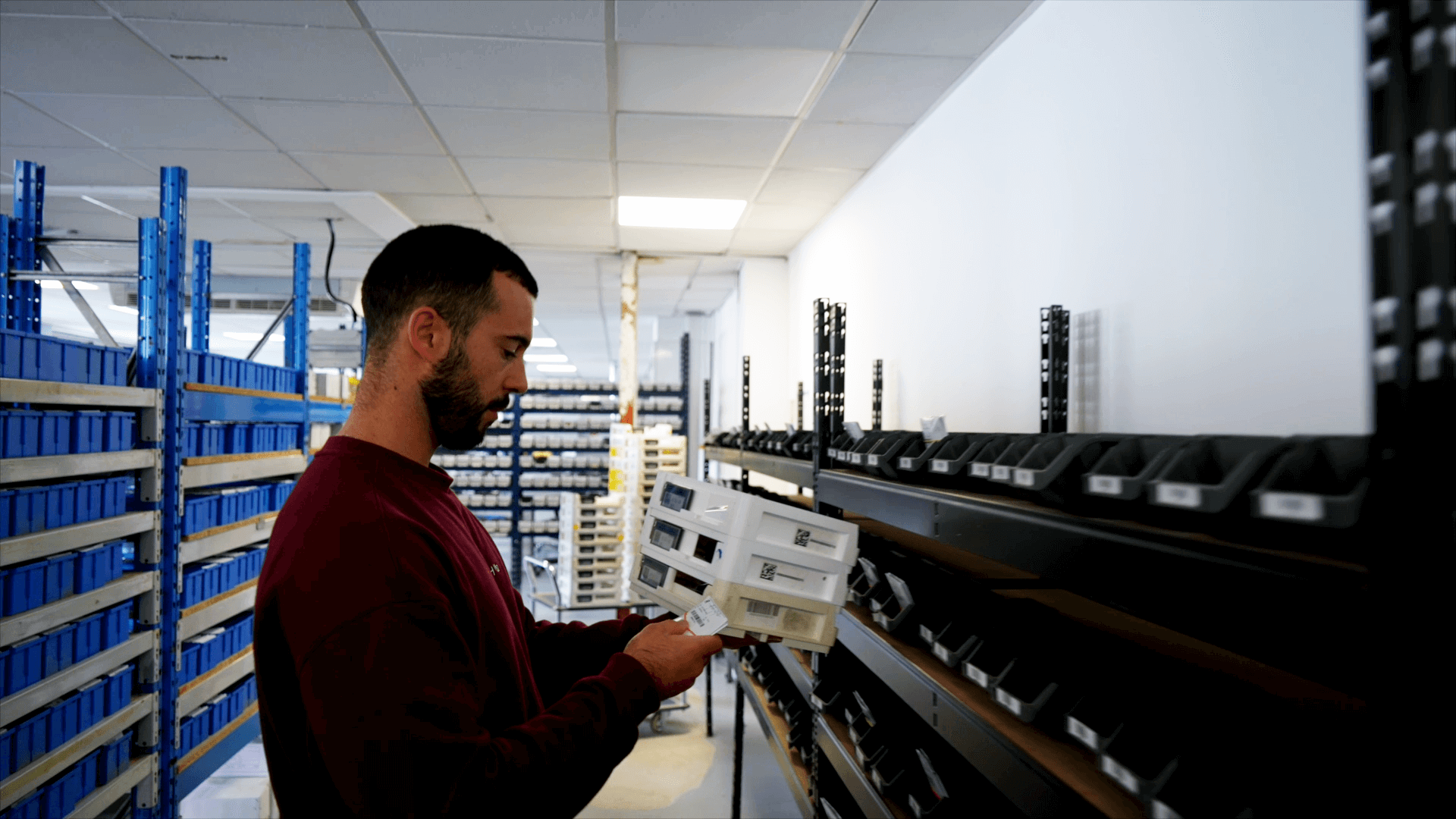
We’ve practically eliminated paper. The environmental impact is profound, and it’s also more cost-effective.
Sustainable and Cost-Effective Gains
With the switch to paperless job tickets, Jimmy Fairly Lab reduced its annual paper consumption by approximately 800,000 sheets, a figure that would have only increased with the company’s growth.
Productivity and Customer Service Wins
Implementing the E-Ticket has optimized productivity, saving the lab the equivalent of two full-time roles. The investment paid off in just nine months, with significant benefits in workflow and order prioritization.
Saved 800,000 Sheets Paper Per Year
Freed Up 2 Full-Time Positions
9 Months
Investment Payback
A Reliable Solution for Scaling Labs
The E-Ticket system has seamlessly integrated into Jimmy Fairly’s processes, proving to be both reliable and user-friendly. “With WiFi and a stable server, the E-Ticket just works,” Manuel notes. “What’s impressive is the transparency for employees-our team adapted immediately without questions or concerns.”
Reflecting on the integration, Manuel advises future adopters to focus on defining essential information for
job tickets.
We reviewed what we actually needed on our production orders and created tailored templates. That’s what makes the E-Ticket so successful for us it’s streamlined to deliver exactly the information we need, nothing more.
The E-Ticket has been completely transparent for our production team. Urgent orders are now easier to track, making it much simpler to expedite them and respond to customer needs more efficiently.
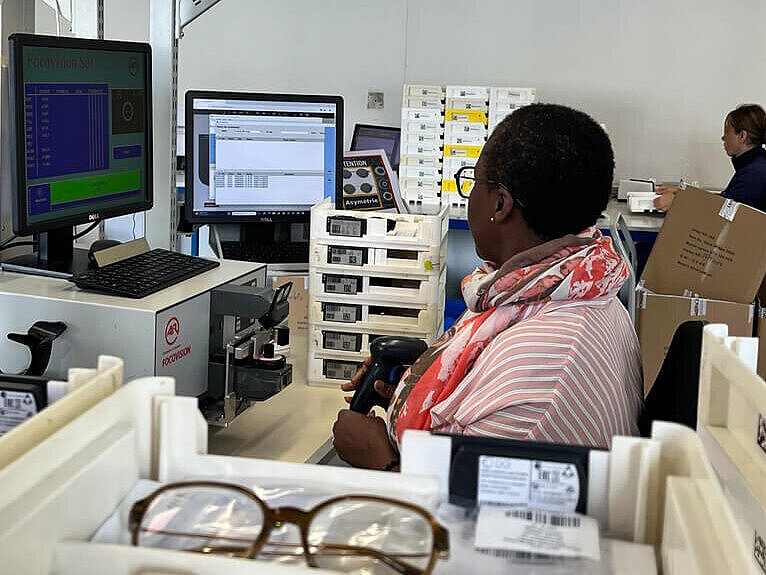
Jimmy Fairly Lab’s partnership with Satisloh is a testament to the brand’s commitment to sustainability, efficiency, and customer satisfaction, delivering responsible and fashionable eyewear with precision and care.
Scaling Production with Smart Automation
Efficiency isn’t just about speed — it’s about smart use of space, seamless workflows, and reducing manual handling. To meet the growing demand of their 148 boutiques across Europe—Jimmy Fairly Lab took a strategic approach to optimize their production workflow. After successfully installing e-Ticket System, which eliminated paper job tickets and streamlined job tracking, the next step was to tackle the manual handling of the job trays without increasing in people labor.
By investing in Satisloh’s Integrated Smart Conveyor (ISC) with MES-360 Routing, Jimmy Fairly Lab was able to automate the routing of the job trays based on machine status and process capability. The result? A smarter, more responsive production flow that adapts in real-time.
With this next-level automation, Jimmy Fairly Lab ensures faster production times, fewer errors, and a seamless manufacturing workflow.
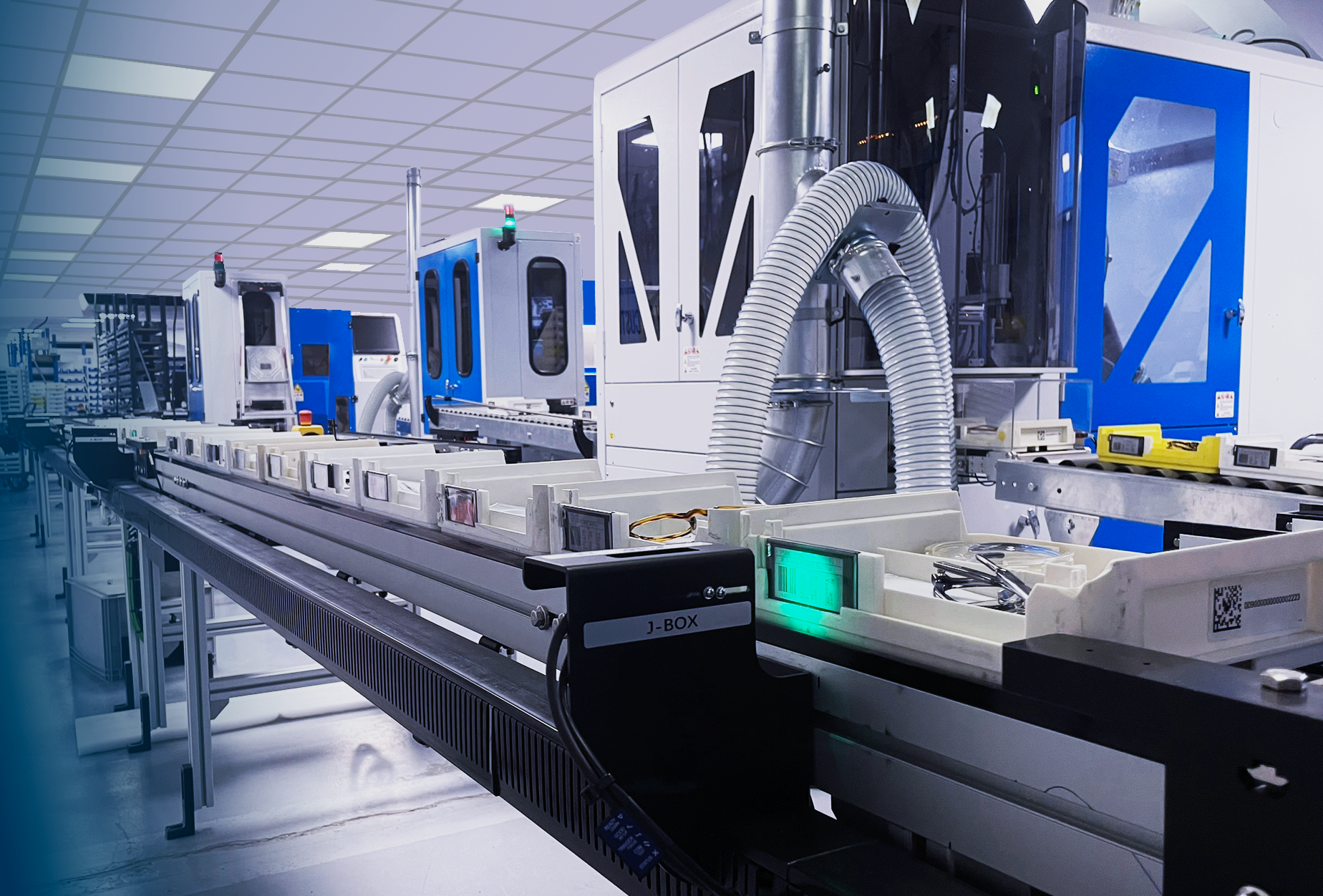
The results so far
Optimized use of Space
–
Maximizing workflow efficiency
Intelligent Routing
–
MES-360 Routing sends trays to the best available machine, reducing bottlenecks
Hands-Free Tray Transport
–
No more manual job tray handling, reducing time and staff can focus on higher value tasks
Scalability
–
A future-proof setup that can grow with the growing production demands
Ask us a question
Satisloh experts are ready to answer your questions. We help you make the right machine purchase decision
Request product information
Satisloh designs and manufactures machines that meet your specific requirements. Request more product information or your personalised quote today!