L'art de la génération ophthalmique
Un défi technologique
La capacité de voir clairement est l'un des aspects le plus important dans notre vie. Qu'il s'agisse de travailler, de jouer, de lire ou d'effectuer des activités quotidiennes, pour beaucoup, cela implique de porter des lunettes. La planète compte plus de sept milliards d'habitants et on estime que 4,6 milliards d'entre eux ont besoin de lunettes, indépendamment de leur sexe, de leur âge ou de leur origine ethnique. Pour ces personnes, trouver la bonne paire de lunettes signifie se rendre chez un opticien de confiance qui commande ensuite généralement les verres à un laboratoire de fabrication ophtalmique.
Au cours des 15 à 20 dernières années, l'industrie ophtalmique a considérablement évolué en raison des nouveaux développements, des nouvelles technologies et des nouvelles conditions de fabrication des verres.
Changements de matériaux
Jusque dans les années 1960, seul le verre minéral était transformé. Aujourd'hui, le verre organique est le principal matériau utilisé pour les verres. Seuls 10 à 15 % des verres actuels sont en verre minéral. Le confort du porteur, le gain de temps, les options technologiques plus nombreuses et les raisons esthétiques sont les principaux facteurs de la domination du matériau organique aujourd'hui.
Évolution des besoins en matière de correction
Outre les besoins en verres unifocaux (pour corriger la myopie, l'hypermétropie ou l'astigmatisme), les besoins en verres supplémentaires pour corriger la presbytie ont considérablement augmenté. Les opticiens peuvent proposer des verres bifocaux, trifocaux et progressifs. S'ils corrigent tous la presbytie, les verres progressifs éliminent les lignes visibles des verres à double foyer traditionnels et des trifocaux et cachent le fait que le porteur a besoin de lunettes de lecture. Dans le domaine des verres progressifs, la technologie a énormément évolué.
Il y a près de vingt ans, toutes les corrections de la presbytie avec des verres progressifs étaient effectuées sur la face avant du verre. Cela offrait des options technologiques limitées et nécessitait des verres progressifs semi-finis dans des stocks importants. Aujourd'hui, grâce à la "technologie freeform" (également appelée surfaçage numérique), toutes les corrections, y compris celles de la presbytie, peuvent être effectuées sur la face arrière du verre. La technologie freeform est en passe de devenir la méthode préférée de fabrication des verres, grâce à un processus de fabrication numérique révolutionnaire et à un équipement de pointe pour la conception et le surfaçage numérique des verres, afin de créer des verres de lunettes personnalisées de haute qualité avec une prescription unique.
Lors de la fabrication des verres, une série d'étapes sont suivies, du blocage à la finition, en passant par la génération, le polissage, le déblocage, le nettoyage et le revêtement. Le processus qui ajoute la ''correction'' sur le verre c'est la génération.
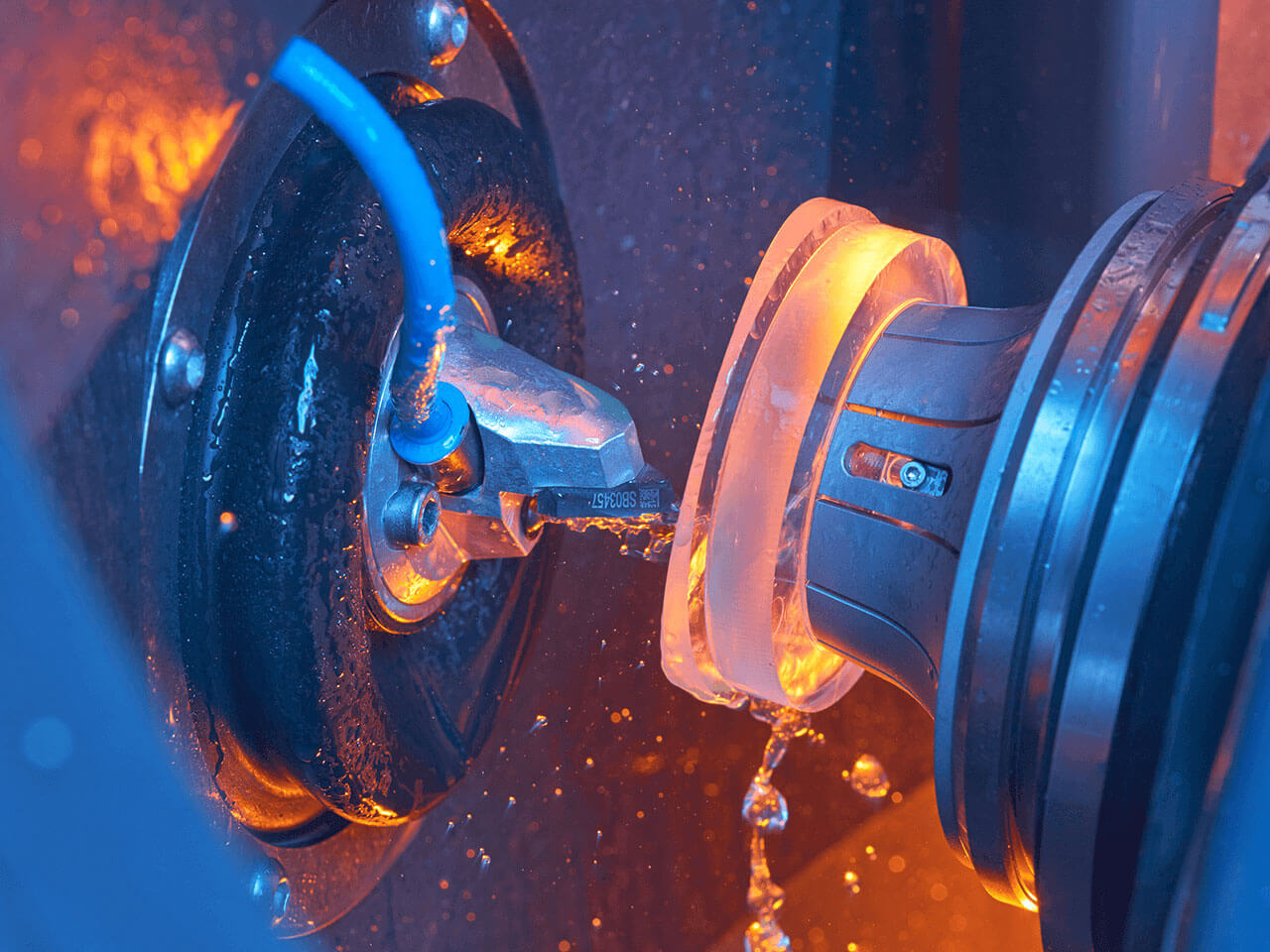
Qu'est-ce qui se passe pendant la génération et comment cela fonctionne?
Après le blocage, le verre est envoyé au générateur qui peut produire des prescriptions avec une précision de 1/100e de dioptrie. Dans le générateur, l'ébauche (verre brut), subit deux étapes différentes - le fraisage et le tournage. La face arrière du verre est traitée et reçoit les informations de correction. L'ensemble du processus ne prend que 35 à 140 secondes, en fonction de la machine et de l'ordonnance à fabriquer.
La génération - le processus de fraisage
Lors du fraisage à grande vitesse (cribbing et surfaçage grossier), la surface du verre est préparée grossièrement. En quelques secondes, la fraise enlève la majeure partie du matériau, réduit le diamètre, biseaute le verre et crée la forme initiale de la surface. La broche de fraisage la plus rapide du marché enlève la matière à 35 000 tours/minute et termine le processus en 7 à 10 secondes environ.
Après le fraisage, un processus de tournage est nécessaire pour lisser la surface avec une coupe finale.
Génération - processus de tournage
Le processus de tournage, également appelé coupe à grande vitesse, prépare la surface de sorte que seul un léger polissage (lustrage) est nécessaire par la suite. Le processus de tournage diffère d'un fabricant à l'autre et d'une machine à l'autre. Les outils de tournage spéciaux dotés de systèmes de commande à grande vitesse offrent une vitesse maximale ainsi qu'une précision de forme et une douceur de surface sans précédent.
Un diamant, situé sur le porte-outil de tournage, est utilisé pour enlever de la matière. En fonction du matériau du verre, on utilise soit un MCD (diamant monocristallin), soit un PCD (diamant polycristallin). Le porte-outil portant le diamant se déplace d'avant en arrière pour générer la surface du verre. Le verre lui-même tourne également à une vitesse pouvant atteindre 4 500 tr/min. Un autre axe d'alimentation déplace l'axe de rotation avec la lentille vers l'arête de coupe de l'outil.
Au cours de ce processus, une accélération de 200 m/s2 peut être atteinte. Cela correspond à vingt fois l'accélération due à la force de gravitation terrestre (connue sous le nom de "g")! Les générateurs traditionnels coupent sur trois axes simultanément, alors que le surfaçage numérique nécessite au moins quatre axes. Il y a un énorme défi technologique, pour gérer au mieux le positionnement des axes pendant le processus de tournage à grande vitesse, en assurant une précision de surface de l'ordre du µm.
Chambre de travail
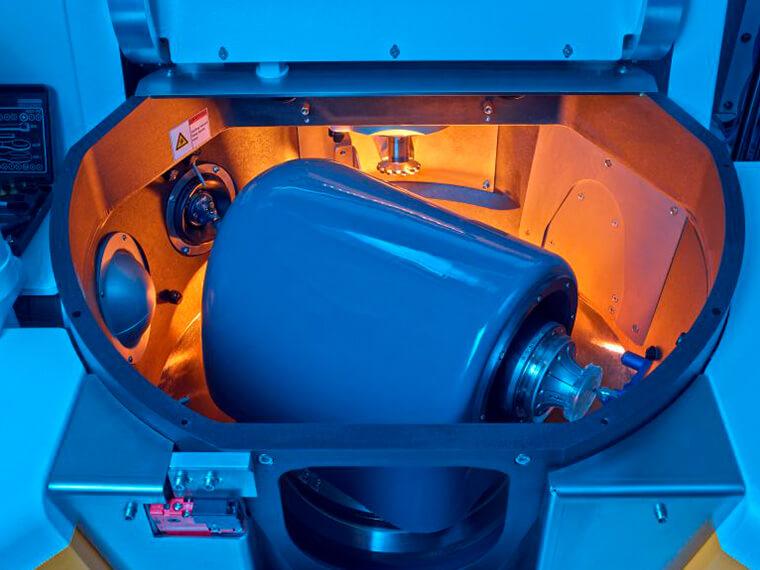
Fraisage à grande vitesse
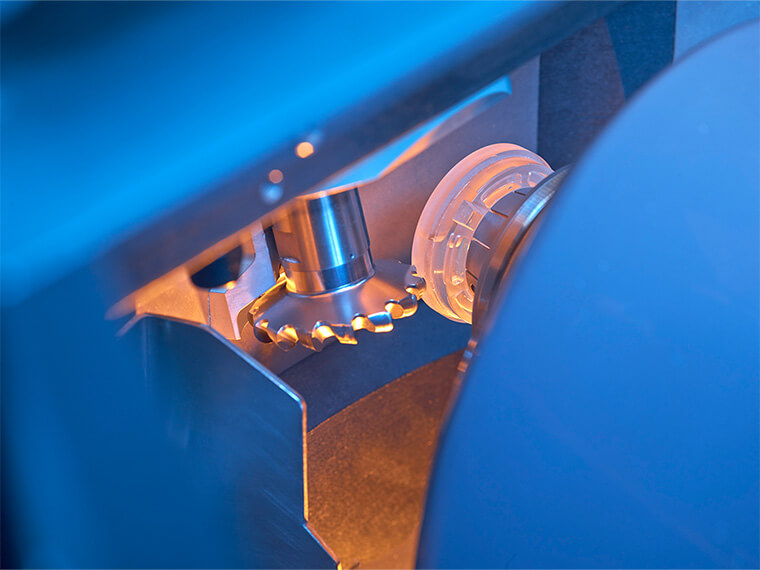
Rotation de précision
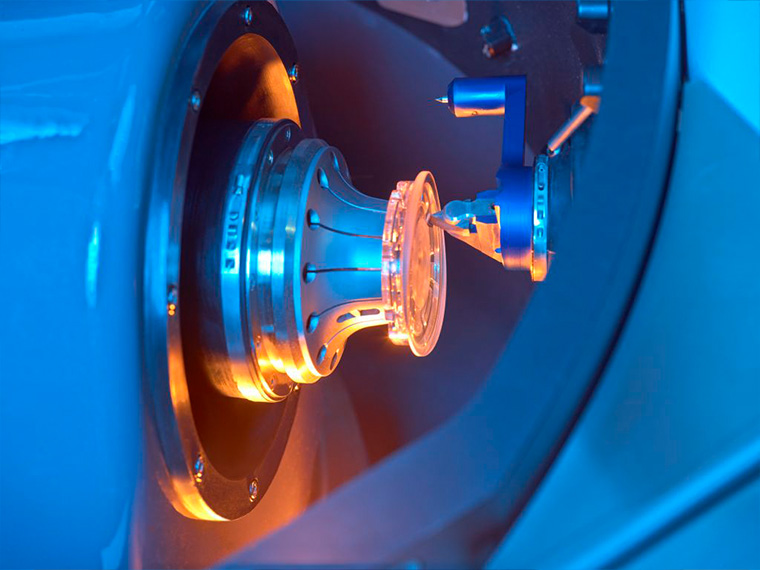
Gravure mécanique
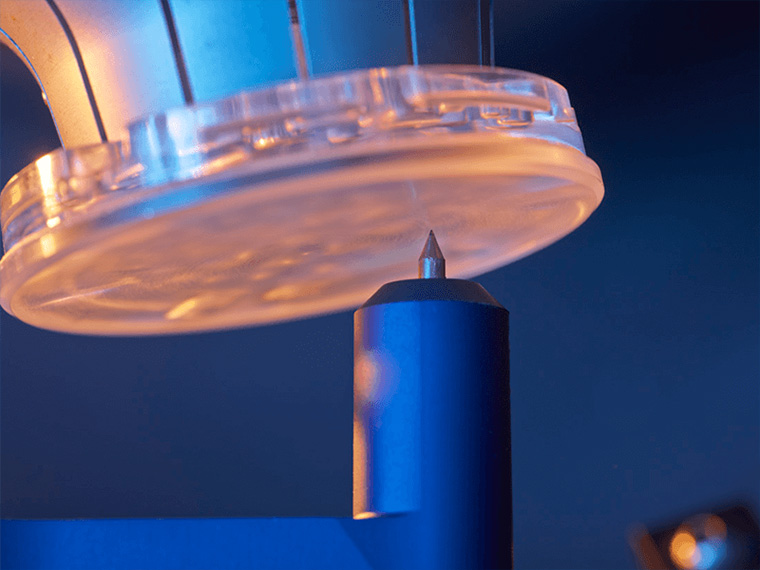
La technicité derrière le technique
Pour garantir les meilleurs résultats en un minimum de temps, il est nécessaire de procéder à des réglages de la machine, tant en fraisage qu'en tournage. Et le mot clé ici est la "distance spirale" qui détermine la distance entre les tours de spirale des coupes finales (à la fois pendant le fraisage et le tournage). Plus cette distance est faible, plus la surface sera lisse pour le polissage. Toutefois, il faut tenir compte du fait que plus la distance entre les spires est faible, plus le processus de génération est long.
Fonctionnalités optionnelles pour la génération
En fonction des exigences du laboratoire ou des spécifications du verre, certaines caractéristiques supplémentaires et optionnelles de la machine peuvent être nécessaires. L'option d'auto-calibrage garantit la qualité de fabrication de la machine. Pour valider les verres après le surfaçage, certains générateurs sont équipés d'une option de mesure de topographie intégrée. Cela garantit une qualité supérieure des verres et simplifie le travail de l'opérateur. Un outil capteur spécial lit la surface du verre et mesure environ 300 points. Les valeurs réelles sont ensuite comparées aux valeurs de référence et l'opérateur reçoit des informations sur la qualité du verre, ce qui lui permet d'adapter la configuration de l'axe de la machine ou la géométrie de l'outil. Certains verres peuvent nécessiter des marquages semi-visibles sur la surface. Il existe différentes méthodes de marquage: une machine séparée (graveur laser) après le polissage, ou un marquage effectué dans le générateur. Étant donné que le débit, les caractéristiques et les niveaux d'automatisation des générateurs varient, les laboratoires doivent choisir un générateur en fonction de leurs besoins spécifiques. Le marché offre des machines avec des débits de production d'environ 25 verres/heure jusqu'à 100 verres/heure.
Maître dans l’art de fabriquer des verres
Enfin, d'un point de vue technologique et mathématique, la génération peut être considérée comme une discipline majeure dans la fabrication des verres. Mais sans une intégration complète et un lien optimal avec tous les autres processus de fabrication de verres, elle serait inutile. Au fur et à mesure que la technologie se développe, le processus de génération continuera d'évoluer. L'industrie favorisera les avancées technologiques et le consommateur en bénéficiera en fin de compte.
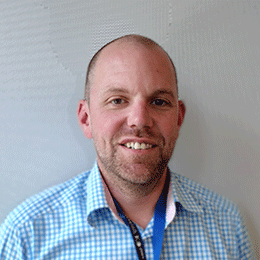
Un article de:
Mark Hollmann
Responsable de la gestion des produits