Brillengläser – Die Kunst der Oberflächenbearbeitung
Technologische Herausforderungen
Klare Sicht – ein Muss bei der Arbeit wie auch in zahlreichen Aspekten unserer Freizeit. Geschätzte 4,6 Mrd. Menschen, gut 60% der Weltbevölkerung, haben eine Fehlsichtigkeit, sind kurz-, weit-, stab- oder alterssichtig. Für scharfen Durchblick sorgen die richtigen Brillengläser. Tut es kein Standardglas, wird nach Verschreibung gearbeitet: Sehtest beim Augenoptiker, individuelle Maßarbeit im Fachlabor. Was genau geschieht in diesen Laboren?
Eine ganze Menge, wobei es über die vergangenen 15 bis 20 Jahre wichtige Neuerungen gegeben hat. Sehen wir genauer hin.
Ausgangsmaterial
Brillenglas – der Name trügt. Bis zu den 1960er Jahren war Mineralglas die Norm, doch bei 85% bis 90% aller Brillen wird heute mit Kunststoff gearbeitet. Tragekomfort, Bruchsicher-heit, Ästhetik, auch die flexiblere, schnellere Verarbeitung sprechen klar für dieses organische Material.
Gleitsichtgläser – alles in einem
Interessant ist auch die Technologie, die dahintersteht. Noch bis gegen die Jahrtausendwende entstand die gesamte Gleitsicht-fläche auf der Glasvorderseite. Dies erforderte große Bestände an vorderseitig bearbeiteten Rohlingen, an denen dann noch die gewohnten rückseitigen Arbeiten vorgenommen wurden. Individualisierung? Fehlanzeige. Und dann kam die Freiformbe-arbeitung ins Spiel. Sämtliche Zonen – Nah-, Zwischen- und Fernbereich – können damit rückseitig herausgearbeitet werden.
Beim Design wie auch der Fertigung kommen raffinierte digita-le Verfahren zum Einsatz, die von der Gesichtsform über die Sehgewohnheiten hin zur Brillenfassung die unterschiedlichsten Faktoren berücksichtigen. Eine Brille, die sitzt wie ein Maßanzug.
Doch was meinen wir genau, wenn wir von Fertigung sprechen? Vom Blocken über das Generieren, Polieren, Abblocken, Reinigen und Beschichten hin zur Randbearbeitung müssen zahlreiche Abläufe ineinandergreifen. Das A und O ist das Generieren. Hier entsteht die präzise Form, die das jeweilige Auge wieder scharf sehen lässt.
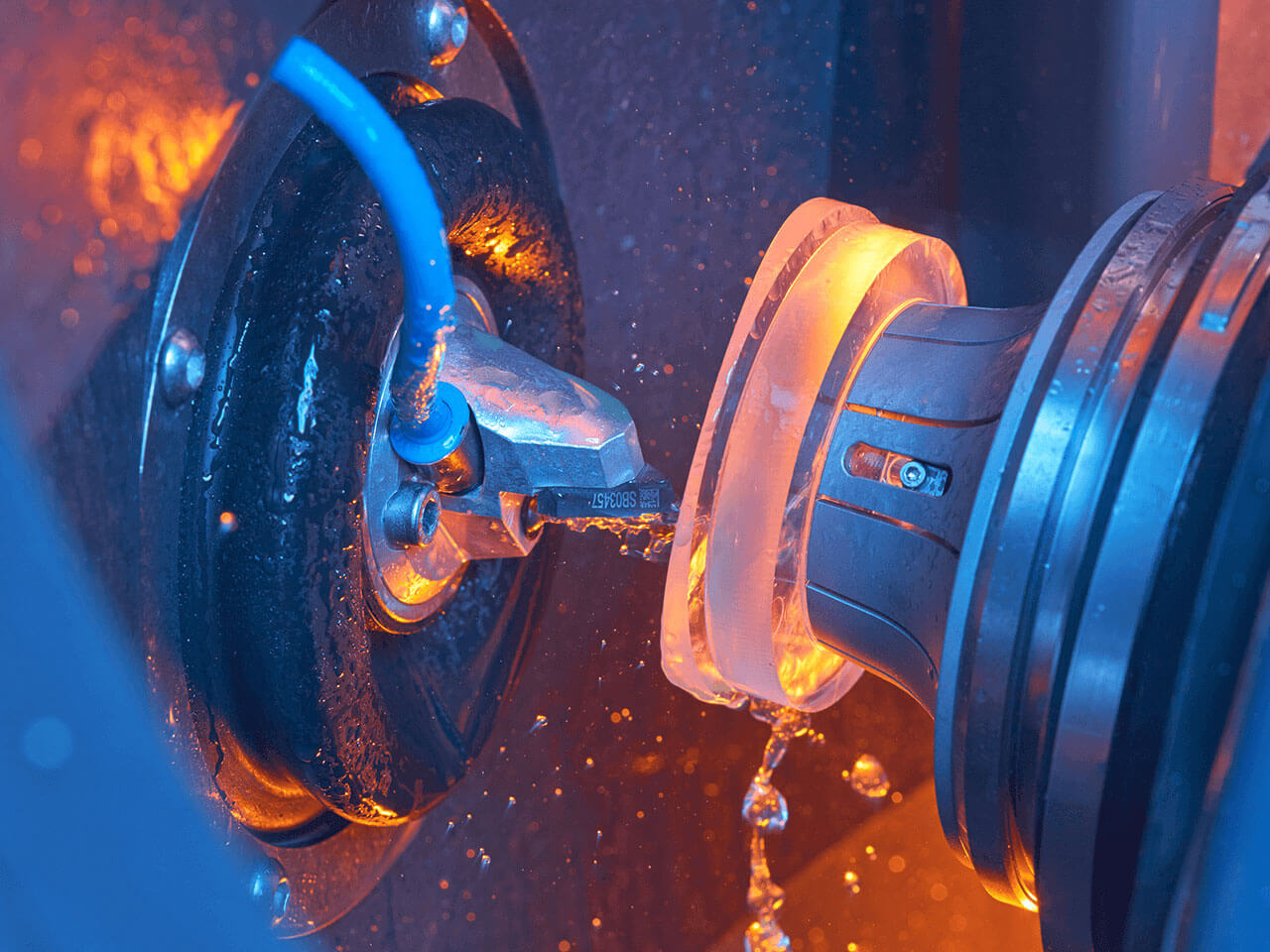
Generieren – was und wie?
Nach dem Blocken, bei dem der Rohling mit einem Blockstück verbunden wird, geht es zur Oberflächenbearbeitungs-maschine, dem Generator. In zwei Schritten, Fräsen und Drehen, werden die gewünschten Brechwerte auf der Glas-rückseite hergestellt – bis auf 1/100 Dioptrie genau. Komplex, aber blitzschnell: Je nach Maschine und Rezept dauert der Vorgang 35 bis 140 Sekunden.
Generieren: Fräsen
Eine Hochgeschwindigkeitsfräse leistet die vergleichsweise „gröbere“ Vorarbeit. Durch Abzentrieren auf Durchmesser und Facettieren wird der Großteil des Materials abgetragen, um die grundlegende Form herauszuarbeiten. Die schnellste auf dem Markt erhältliche Frässpindel erledigt dies bei 35.000 Umdre-hungen pro Minute (min - 1) in 7 bis 10 Sekunden. Die nun noch etwas raue Oberfläche muss durch Drehen geglättet werden.
Generieren: Drehen
Nach dem Feindrehen ist die Rautiefe so gering, dass nur noch ganz leicht poliert werden muss. Die genauen Abläufe sind je nach Hersteller und Maschine unterschiedlich. Spezielle Drehmeißel in Kombination mit Hochgeschwindigkeitsregelsystemen ermöglichen Spitzengeschwindigkeit bei höchster Formgenauigkeit und Oberflächenglätte.
Als Schneide dient ein Diamant, der je nach Glasmaterial monokristallin (MKD) oder polykristallin (PKD) sein kann. Dieser fährt am Werkstück hin und her (Vorschubachse), das wiederum mit bis zu 4.500 min -1 um die eigene Achse rotiert (Rotationsachse). Eine dritte Achse, die Zustellachse, bestimmt die Schnitttiefe, d. h. den Eingriff der Schneide in das Werkstück.
Achsbeschleunigungen von bis zu 200 m/s2 können dabei erzielt werden – das 20-Fache der Fallbeschleunigung (g) aufgrund der Erdanziehung! Drei Achsen, so weit ganz überschaubar. Zumindest eine weitere Achse ist jedoch zur Freiformbearbeitung erforderlich. Die korrekte Achspositionierung, die perfekte Abstimmung all dieser simultanen Bewegungen, ist und bleibt eine technologische Herausforderung – zumal bei Toleranzen im μm-Bereich.
Die Technik hinter der Technik
Beide Vorgänge, Fräsen und Drehen, erfordern eine ausge-klügelte Maschinensteuerung. Von größter Bedeutung ist der „Spiralabstand“: Je kleiner die Abstände zwischen den spiralförmig verlaufenden Schnittlinien, desto glatter die entstehende Oberfläche, desto einfacher das anschließende Polieren. Andererseits bedeuten kleinere Abstände natürlich auch längere Bearbeitungszeiten. Hier gilt es genau den rich-tigen Kompromiss zu finden.
Generieren: optionales Zubehör
Doch der Generator selbst ist erst der Anfang. Je nach den Anforderungen des Labors (oder seiner Kunden) können viel-fältige Optionen hinzukommen.Da wäre beispielweise die automatische Kalibrierung. Abweichungen, die sich an den Achsen und dem Werkzeug nach und nach einschleichen, werden erkannt und kompensiert.
Einige Generatoren ermöglichen auch eine integrierte Topografiemessung. Ein Sensor analysiert die bearbeitete Glasoberfläche anhand von rund 300 Bezugspunkten. Die so bestimmten Istwerte werden mit den spezifizierten Sollwer-ten verglichen. Der Bediener erhält einen QA-Bericht und kann schnell und sicher die nötigen Korrekturen an der Achs-konfiguration und/oder Werkzeuggeometrie vornehmen – konstante Spitzenqualität vorprogrammiert.Die Gläser sollen signiert werden – etwa mit dem Logo des Herstellers oder den Initialen des Endkunden, sichtbar oder nahezu unsichtbar? Manche Generatoren können dies direkt übernehmen. Zudem gibt es separate Lasergravierer, die nach der Politur ansetzen.
Eines ist sicher: Generator ist nicht gleich Generator. Durchsatz, Einsatzmöglichkeiten, Grad der Automatisierung – bei all diesen Faktoren gibt es erhebliche Abweichungen.
Generieren – die Königsdisziplin
Von welcher Warte auch immer, fertigungstechnisch, mathe-matisch, optisch: Das Generieren ist bei der Brillenglasferti-gung die Königsdisziplin. Doch der Generator steht nicht für sich allein. Vom Blocken zur Randbearbeitung müssen alle Abläufe perfekt ineinandergreifen. Am besten, alle Maschinen werden aus einer Hand bezogen. Und dann heißt es am Ball bleiben: Bei dem hohen Innovationstempo gibt es stetige Fortschritte, die allen Beteiligten zugutekommen – Laboren, Augenoptikern und nicht zuletzt den Brillenträgern.
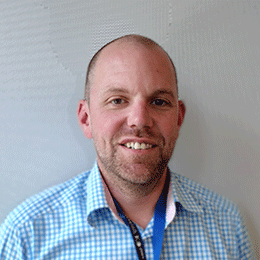
Ein Artikel von:
Mark Hollmann
Head of Product Management